Products
Our custom products and solutions are not only engineered to the exacting specifications of our customers, but designed to perform under the harsh conditions of today’s advanced manufacturing processes.
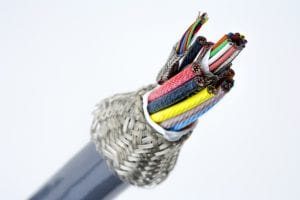
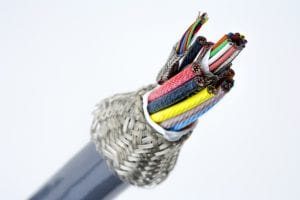
Multi-Conductor Cables
Incorporating multiple conductors into one cable for the ultimate in customization and usage flexibility
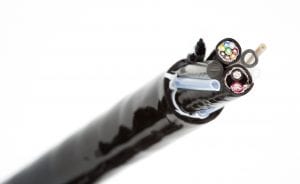
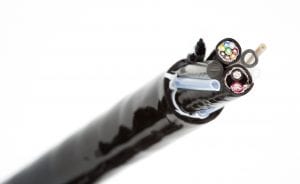
Hybrid Cable Configurations
We design custom cables incorporating dissimilar components for maximum functionality in the same cross-sectional area.
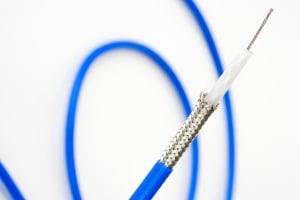
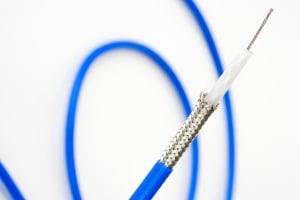
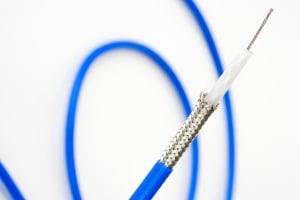
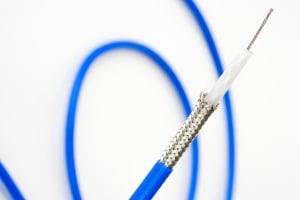
Coaxial Cables
We recognize the importance of transmission line performance for maximizing signal quality in high-frequency systems.
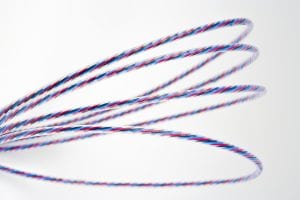
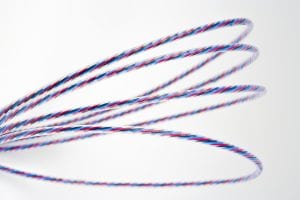
Twinaxial Cables
When signal integrity is of the utmost importance, we can design and manufacture twinaxial cable to meet the characteristic impedance, capacitance and attenuation requirements of your application.
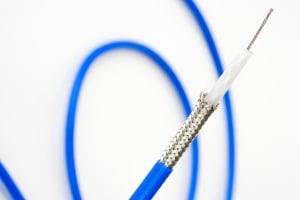
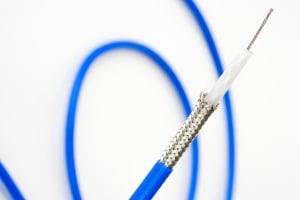
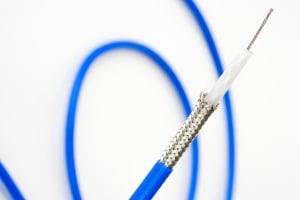
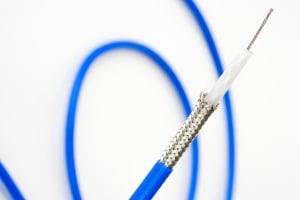
Miniature and Micro-Miniature Coaxial Cables
Manufacturing miniature coaxial cable requires precision equipment and a depth of expertise that has been a hallmark of New England Wire Technologies since our founding.
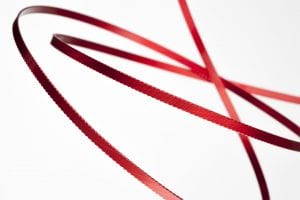
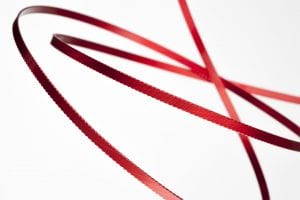
Litz Wire Types and Constructions
A description of the various styles of Litz wire – Type 1 through Type 9
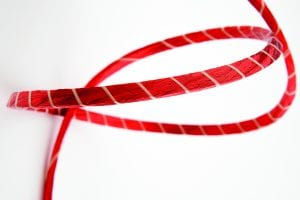
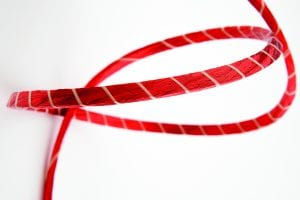
Custom Litz Wire Options
We have extensive experience with Litz wire manufactured from custom materials and insulations.
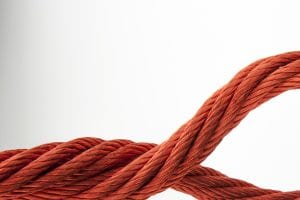
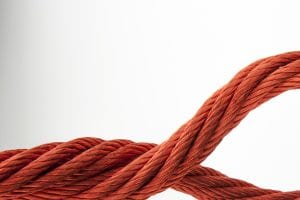
Round Litz Wire
Litz Types 1 through 6, and also 9, are all designed to be round and vary from a simple bunch of conductors to complex designs utilizing multiple cores and several manufacturing operations.
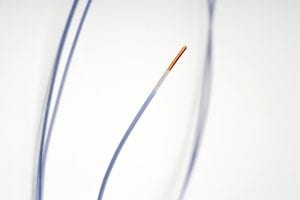
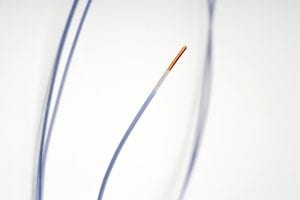
NEWind® Double and Triple Insulated Winding Wires
NEWind® is a high end multi-layer winding wire that replaces traditional forms.
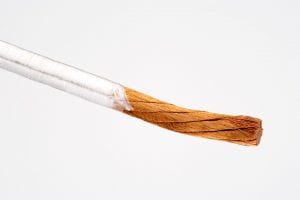
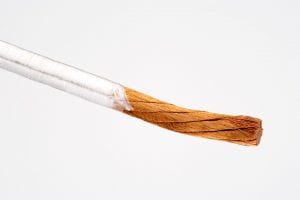
NE-F1 Class F (155°C) Electrical Insulation System
Use our EIS to eliminate the need for long term component testing
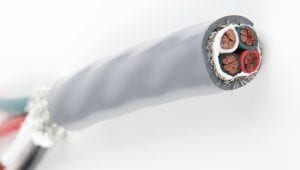
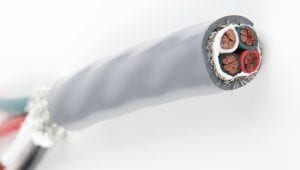
Multi-Conductor Cable for Extreme Temperatures
We offer a full range of products to meet requirements from cryogenic to 450°C and beyond.
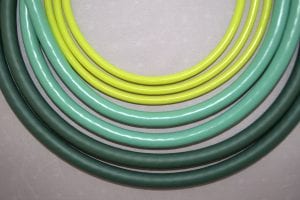
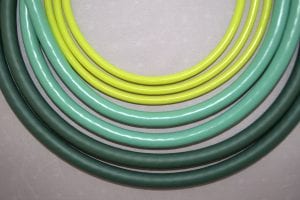
Custom Flexible Interconnects
Design considerations and options for your custom configuration
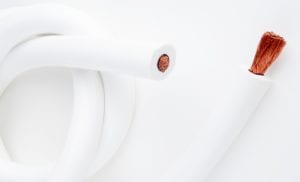
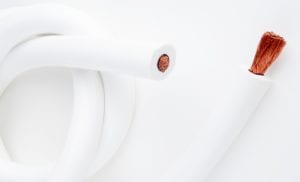
Extended Flexlife Cables
Design options for extreme flexibility and long-term flex life
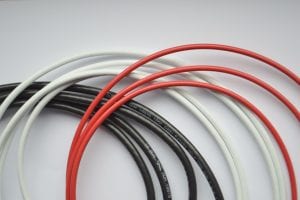
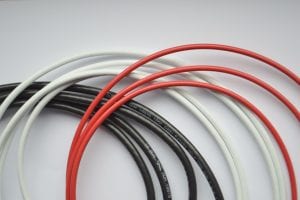
General Purpose Power Leads
We manufacture general purpose power leads and lead wires using a range of wire gauge sizes, strand constructions, conductor materials, wall thicknesses, and jacket insulations.
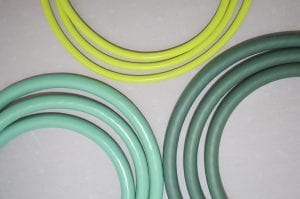
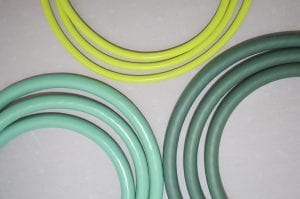
Styles For Power Leads
We manufacture a wide range of power leads with component recognition to UL and CSA for OEM installation.
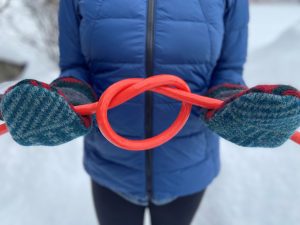
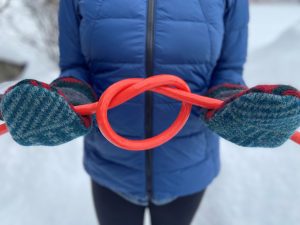
COLDflex Ground Cable™
Specifically designed for flexible, low-temperature ground cable applications
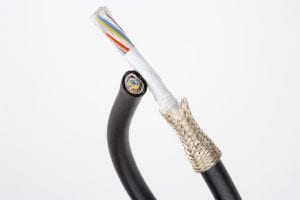
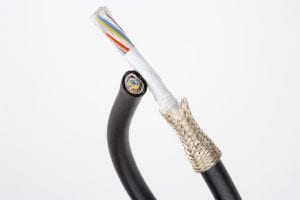
NEWtuf® Reinforced Silicone Rubber Cables
NEWtuf® reinforced jackets provide three times the tensile strength of silicone rubber and limit elongation distortion to a fraction of a percent.
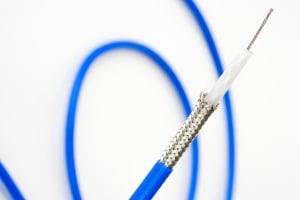
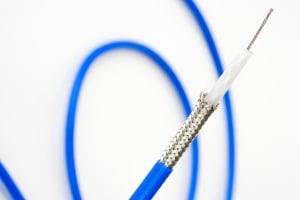
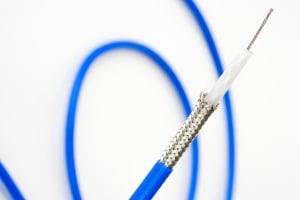
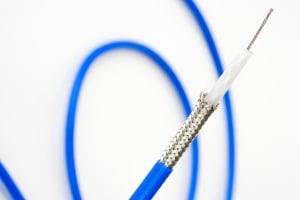
NEWcel® Foamed Dielectrics
Our proprietary closed-cell foamed dielectric material designed to significantly reduce dielectric constant without sacrificing structural integrity
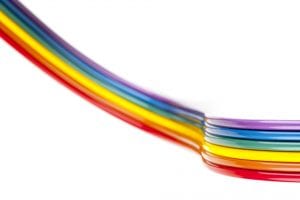
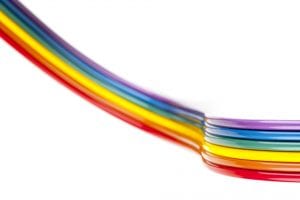
Ribbon Cables and Zip Cords
Ribbon cables are made by jacketing multiple legs in a single extrusion process creating a cable of high single dimension flexibility that has easily separated sub-components.
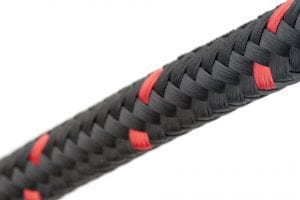
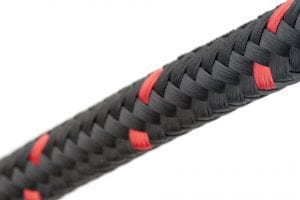
Custom Braids
High-quality braided products are part of our long history of excellence.
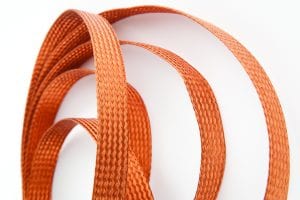
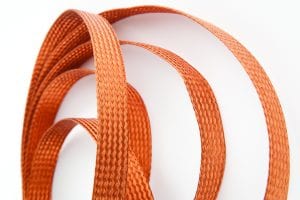
Flat and Wide Braids
We manufacture flat and wide braids in a vast selection of materials and constructions
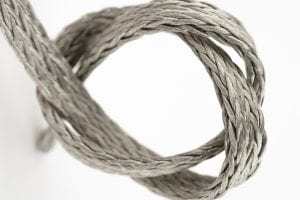
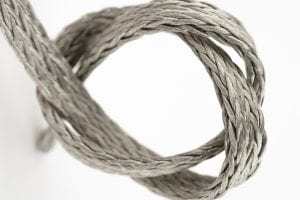
Shielding Braids
Reduce electrical interference and provide mechanical protection for your cable
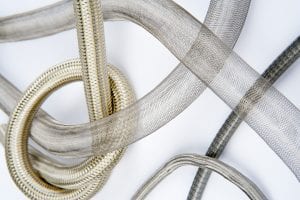
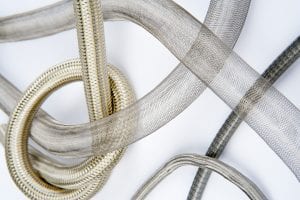
Medical Braids
New England Tubing Technologies, a subsidiary of New England Wire, draws on a unique combination of core technologies to design and produce high quality, custom medical braiding.
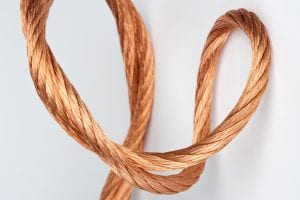
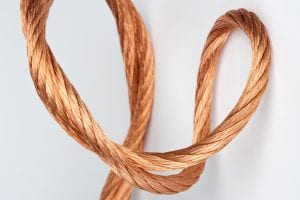
Ultra Flexible Strands
For applications where flexibility and extended flex-life are primary concerns
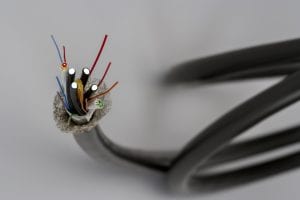
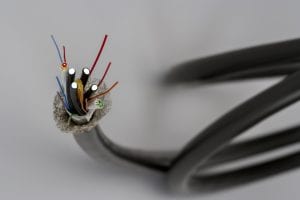
Customer Supplied Materials and Toll Orders
We are happy to incorporate customer-supplied materials into your custom cable project
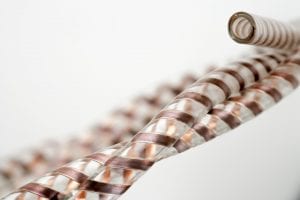
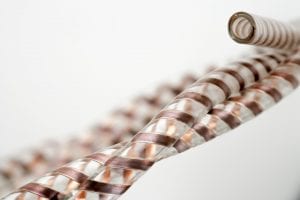
Custom Reinforced Tubes
Our subsidiary, New England Tubing Technologies works with clients to custom design products based on the unique product performance characteristics required.