As advances in artificial intelligence (AI) continue to multiply, robots are getting smarter and more capable. Early robots like those massive machines used in 1970s automobile manufacturing were controlled by software that directed their repetitive behavior. Such robots were dangerous to humans because they were strong, moved quickly and could easily cause bodily harm. Hence, they were kept in cages, away from workers. Now though, artificial intelligence is giving robots the ability to monitor the environment and adjust their behavior accordingly. Human-robot collaboration and even robot-robot collaboration is becoming commonplace.
There’s a curious thing that happens as a technology develops, and it’s happening at breakneck speed with AI and robotics. To illustrate the point with an example, consider GPS navigation, another technology that has evolved dramatically. GPS was launched by the U.S. military in 1973, made available to the public in the 1980s and found its way into Garmin, Magellan, Tom Tom devices and cell phones in the mid-2000s.
One of the earliest GPS receivers was the U.S. Army’s PSN-8 Manpack GPS Receiver. It weighed 17 pounds and required the operator to use a 24-button keypad to get readings. Today, our cell phones guide us to our destination with a spoken command or a touch or two on the screen. We’ve come to take that simplicity for granted.
However, for GPS navigation to have reached today’s ease of use and compact form factor, an entire host of technologies had to be invented, then perfected. The GPS receiver inside a cell phone had to be shrunk from 17 pounds to the size of a tiny silicon chipset. Antenna technology had to advance to the point that an omni-directional antenna small enough and with enough gain to detect GPS radio signals could be built into the phone. Voice synthesis technology and voice recognition had to be developed and perfected. The phone’s operating system had to be adjusted to accommodate GPS functionality. All of these and many others—even the invention of semiconductors, integrated circuit chips and surface mount technology—were all prerequisites.
Yet today, especially in the world of software, the pieces of code that do specific functions can be “plugged in,” as it were. Plug in the software that decodes the output of the GPS receiver. Snap in the voice recognition software and voice synthesis code. Each of these proven pieces of code have become building blocks in the overall system, eliminating the creative but difficult and time-consuming engineering task of developing the system from scratch. In short, this “plug in tech” speeds the development of technology, which is why Ray Kurzweil says: “Technology goes beyond mere tool making; it is a process of creating ever more powerful technology using the tools from the previous round of innovation.” That’s exactly what’s pushing the edges of robot development and capability today.
Robotics Software & Connectivity: What’s On the Horizon?
International Data Corporation (IDC), a global market intelligence firm, published its assessment of where robotics is going in the next several years and what impact the field will have on industry and everyday life. According to Jing Bing Zhang, IDC director of worldwide robotics, “Robotics will continue to accelerate innovation, thus disrupting and changing the paradigm of business operations in many industries.”
There’s no doubt robots will impact lower-skilled workers. However, among the developments IDC forecasts, those below suggest robotics and AI will be disruptive in ways yet to be foreseen.
- Robots as a Service (RaaS). The “as a service” concept refers to the practice of organizations subscribing to software delivered via the Internet rather than buying software and installing it locally. By connecting robots to the Internet, they’ll have access to resources and knowledge required to perform specific tasks. For instance, designing a given robot to carry on conversations with humans will not require engineers to build in speech synthesis and voice recognition capabilities. Instead, they’ll make provisions for the robot to download that functionality via the Internet, much like the “plug in tech” concept noted above. And that’s just the beginning.
- Cloud-based services will dominate. IDC claims that by 2020 “60 percent of robots [will] depend on cloud-based software to define new skills, cognitive capabilities, and application programs, leading to the formation of a robotics cloud marketplace.”
- An “Intelligent RoboNet” will evolve. The use of the cloud to expand robot capabilities will, in turn, lead to a robotics cloud marketplace with vendors offering software to give robots an ever-expanding array of skills and abilities. But that’s not all. IDC further predicts that “40 percent of commercial robots will become connected to a mesh of shared intelligence, resulting in 200 percent improvement in overall robotic operational efficiency” by 2020.”
- Robots will expand to many industries. As soon as 2018, the report suggests nearly half of the world’s 200 leading ecommerce and omni-channel organizations will be using robots in their warehousing and order fulfillment operations. Then, by 2019, more than one-third (35 percent) of utilities, logistics and health organizations will be exploring how robots can help them automate internal operations.
What About Robot Hardware?
While software is driving much of the innovation in robotics, robots designed to do work need a physical form and a “nervous system” that connects all its components and sub-systems into a coherent unit that reliably performs various tasks.
A bill of material for a robot typically includes motors and linear actuators, which may be electrical, pneumatic, hydraulic or piezoelectric. Motors usually need motor controllers. Machine vision requires CCD cameras and often LED lighting. These many subsystems need to be connected with wiring and cabling.
Perhaps the most obvious problem engineers have to solve in designing that “nervous system” involves repetitive motion that flexes wires and cables thousands of times in even a single day. Adding to this challenge, wires and cables must often be routed in tight radius bends and must withstand vibration.
At New England Wire we aim to assure high performance for every specific application. In the case of robotics, we’ve found the choice of wire gauge, cable jacketing, and overall cable design each contribute to durability. In particular, our extended flex-life cables solve these problems, and are widely used in large scale robotic warehousing and order fulfillment.
Likewise, robots often use hybrid cable configurations where one cable has the components for communication, power, and fluid delivery all within the same cross-section. Customizing cables with high speed serial connectors and data capture in a highly flexible and durable cable is also important in robotics. And, not to be overlooked, for robots that need to recharge themselves periodically, Litz wire is the conductor of choice for wireless charging pads.
New England Wire provides solutions for each of these design issues. We’re already heavily involved in building the “nervous system” for robots, so be sure to contact us to discuss your needs. We welcome the opportunity to work with you in custom-designing the wire and cable you need.
Custom Design
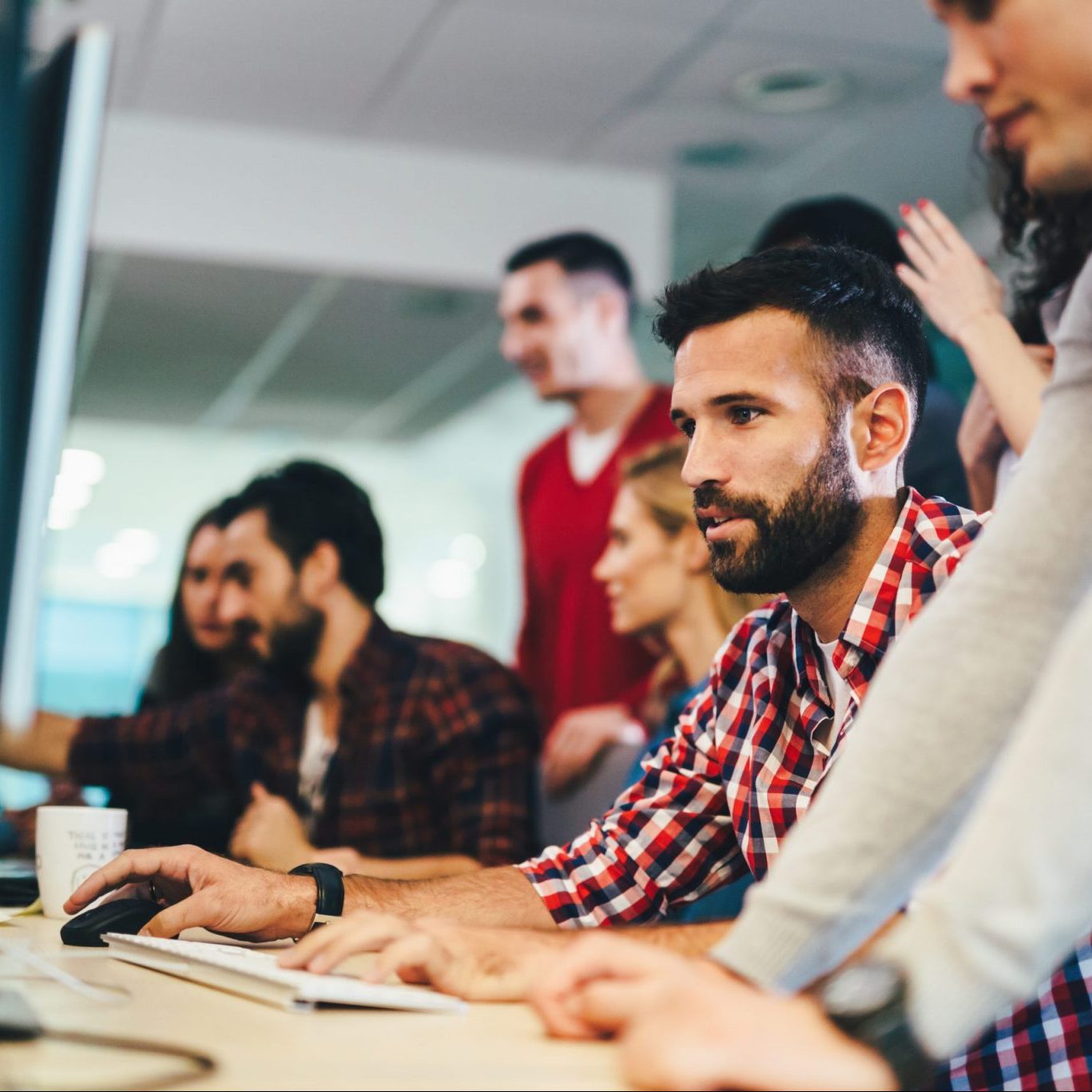
About Our Engineers
Innovative solutions start with an experienced team of engineers, armed with the latest design tools and technology. Our focus on understanding the individual, complex challenges of our customers and designing solutions that fit, is why we have been trusted as the industry leader for over 100 years.