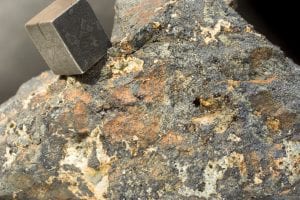
An ancient Greek legend attributes the discovery of magnetism to a shepherd boy who stepped on a rock that attracted the nails in his shoes and the metal tip of his staff. He stumbled on a lodestone, a naturally magnetized piece of the mineral magnetite. Lodestones were sought after in ancient times for their mysterious properties. For instance, a lodestone suspended from a string orients itself to Earth’s north and south magnetic poles, which made lodestones useful for primitive navigation. Today, magnets are used in endless applications ranging from toys and consumer products to medical, scientific and industrial equipment. But perhaps one of the most intriguing applications involves magnetic levitation, also known as maglev.
Maglev technology that has best captured the public’s attention lies with trains and people movers, discussed below. However, maglev tech has many applications. Read about several of the most economically significant applications below and of the role Litz wire plays in many of them.
Maglev Trains Promise Fast, Frictionless Transportation
In the 19th century, Samuel Earnshaw, a mathematical physicist born in England, developed a theorem that came to bear his name. Earnshaw’s Theorem proved that fixed permanent magnets cannot be used to produce a stable repulsive field that allows magnetic levitation. Strangely, scientists of that era failed to notice that the theorem applies only to permanent magnets fixed in a static relationship to one another. Fortunately, some inventors did recognize that limitation, which led them to develop practical designs for magnetic levitation.
Emile Bachelet was one of those. In 1912, he patented his “Levitating Transmitting Apparatus,” which he explained “is a novel apparatus for transferring bodies at very high speed from one point to another, and is particularly designed and adapted for transmitting mail and small express packages long distances at very high speed.” He was the first in the U.S. to envision maglev transport. He demonstrated a model maglev train in hopes of finding investors, but none appeared.
Two decades later, Walter Kemper of Germany made another pitch for maglev transportation, was awarded a German patent, and eventually manufactured a prototype maglev train. Following numerous patents filed up through the 1980s, the first maglev train to see commercial service was a low-speed shuttle that carried passengers between the UK Birmingham airport and the Birmingham railway station beginning in 1984. Following on its heels the same year, the M-Bahn opened in West Germany and ran at speeds up to 260 MPH for a short time, until the reunification of the country rendered it nonessential.
Today, maglev trains serve customers on a daily basis in South Korea, Japan and China, traveling at speeds up to 270 MPH. Dozens of maglev train lines are being planned, discussed, and in some cases, funded, throughout Europe, Asia and the U.S. The need for entirely new rights-of-way and construction cost for the more expensive maglev guide ways has been the biggest drawback to maglev transportation — especially considering that high-speed bullet trains on conventional tracks reach speeds up to 275 MPH, not much slower than maglev.
Two Basic Designs
Maglev trains use two different methods to raise their loads above a “track.” One method known as Electro-Magnetic Suspension (EMS) places electromagnets on bottom surface of the train car that attract the train toward an iron-plate rail above that surface. Current applied to the electromagnets raises the train several millimeters above its rest position. Forward motion is produced by pulsed electromagnets affixed along the length of the carriage which interact with magnets along the rail. In Germany, the demonstration Trans-Rapid TR08 train and its 30 kilometer test track is an example of EMS technology with operating speeds approaching 160 MPH.
The second method is Electro-Dynamic Suspension (EDS), which relies on the principal of superconductivity. Trains using EDS have super-cooled electromagnets along the side of the carriage that interact with figure-eight-shaped electromagnets placed along the length of the guide way. As the train moves, two opposing currents flow through the magnets along the guide way. These create a repulsive magnetic fields that provides lift of several centimeters. Linear synchronous motors provide forward motion. The Japanese SCMaglev uses the EDS approach. This train and others using EDS need to achieve a certain speed before the interaction between carriage and guide way magnets levitates the vehicle. In the case of the SCMaglev, rubber tires driven by electric motors accelerate the train until it achieves levitation.
Magnetic Bearings
Magnetic bearings support moving parts in equipment with no physical contact between the fixed and rotating surfaces. This eliminates mechanical wear and the need for lubrication and maintenance that ordinary bearings require. In turn, magnetic bearings use less energy than traditional bearings. For instance, the US Navy conducted a two-year test and found magnetic bearing saved 40-65% over the original equipment, and reduced maintenance costs. Further, magnetic bearings can operate in a vacuum and other extreme environments. These bearings can be either passive or active.
Passive magnetic bearings (PMBs) use only permanent magnets and therefore require no power. However, Earnshaw’s Theorem says there is no configuration of stationary magnets alone which can keep another magnet in one place. That is, it’s not possible to stabilize two permanent magnets in all degrees of freedom by passive magnetic levitation alone. Therefore, fabricating passive magnetic bearings therefore requires that one of more degrees of freedom be managed by some non-magnetic means. As an example, if two permanent magnets were in the form of rings that could be stacked on a central post held vertically, the post would keep the magnets from flipping over. Similarly, if the post is positioned horizontally, it would have to be secured at either end with jewel-type bearings. That is the approach NASA studied when it began considering PMBs in low earth orbit satellites as far back as 2003. Their G2 flywheel for spacecraft energy storage delivers 535 Watt-hours using a carbon fiber-titanium flywheel designed to spin at 60,000 RPM on a passive magnetic bearing.
Active magnetic bearings (AMBs) use a combination of permanent magnets on the rotating component (rotor), electromagnets on the stator, and control circuitry to control the position of a rotor, for example, in a turbine. The stator surrounding the rotor is fitted with several pairs of electromagnets. They work in concert with position sensors and the bearing control electronics to constantly adjust current flow through the electromagnets. Those magnetic fields interact with permanent magnets on the rotor to keep the rotor in its intended position.
Today’s applications for AMBs is diverse. They are used in many kinds of motors, generators, pumps and turbines, as well as…
- Watt-hour meters
- Centrifugal compressors that power chillers
- Centrifuges used to process uranium, beginning during the Manhattan Project
- Within artificial hearts, as a ventricular assist device
Grid-Connected Flywheel Energy Storage
Grid-connected flywheels perform much the same function as backup battery systems — they regulate and balance the energy available on the power grid. However, they store and supply power using electro-mechanical means. A flywheel powered by a motor-generator spins up the flywheel when run in the motor mode, thereby storing kinetic energy. It returns energy to the grid by transferring that energy when in the generator mode. These flywheel systems are especially effective in smoothing out momentary drops in output from renewable energy sources. When clouds obscure a photo-voltaic solar farm or when wind drops to the point that wind farms cannot operate, flywheel energy fills the short term need — often for up to several hours depending on the demand. Active or passive magnetic bearings allow these devices to run with nearly no maintenance required.
For most of its history, the grid has operated with few practical methods (other than pumped hydroelectric) to store energy. Now though, with the growth of renewable energy — 18 percent came from wind, solar and hydroelectric in 2017 — the need for energy storage is mirroring that same growth curve. In turn, the market for magnetic bearings will continue to grow at a predicted 4.14 percent compound annual growth rate through 2023.
Wind Turbines (Windmills)
With wind farms playing a significant role in renewable energy production, manufacturers have developed both direct drive units that can produce electricity at very low wind speeds, as well as units with gearboxes that can weigh several tons. Over the years, manufacturers have also increased their height, seeking to capture more wind power. At present Germany holds the record for the world’s tallest wind turbine. Its hub is 584 feet off the ground, while the overall height to the tips of the upward-extended blades towers 809 feet above the ground. That turbine has a 3.4 MW capacity, which is about the maximum obtainable from a single turbine today.
However, the most powerful wind turbine to be built is being assembled in central China. Dubbed “MAGLEV: The Super-powered Magnetic Wind Turbine,” its blades are arranged vertically around a central column that uses the repulsive force of permanent magnets. It can generate power with winds as low as 3.3 MPH or as high as nearly 90 MPH — a speed at which traditional wind turbines are taken out of service for safety reasons. It’s expected to deliver 1 GW of capacity, to decrease operating cost by 50 percent and to remain in operation for a staggering 500 years.
Spacecraft Launch
Without any doubt, the most dramatic use of maglev technology would launch spacecraft without the need for expensive rockets. NASA introduced its Space Launch Initiative in 2001, seeking to find new options that would give better access to space. The next year they initiated their Next Generation Launch Technology program that would specifically seek out new ways of moving payloads into space.
By 2010, NASA had evaluated maglev launch concepts and built a prototype launch system at the Marshall Space Flight Center in Huntsville, AL. One design concept uses a 2-mile long track that would accelerate a spacecraft at speeds up to Mach 10, where a small rocket booster would fire the craft into low earth orbit (LEO). Other concepts used scramjets propelled along a maglev track.
With the cost of raising just one kilogram of payload into orbit pegged at about $22,000, new approaches would make space travel far more affordable. For instance, the Saturn V at liftoff weighs more than 3,400 tons, yet can deliver only 120 tons to LEO — just 3.5 percent of its total mass, meaning that 96.5 percent became space junk or fell to the bottom of the ocean.
Another proposal offered to NASA, known as StarTram, would cut the cost of orbiting one kilogram to around $50, thus making launches into space routine. NASA evaluated StarTram in 2005 to uncover flaws in its design concept and found it to be entirely within the capabilities of modern engineering.
StarTram Generation 2 is envisioned to carry humans into space. Accelerating at low g-forces (2 to 3 g), these spacecraft would exit the launch tube at about 14 miles above sea level into the stratosphere. That would require building a launch tube that could be 620 to 930 miles long. The remarkable aspect of this design, beyond its sheer scale, is the method used to suspend the launch tube. Its designers have chosen magnetic levitation over alternatives such as massive, tethered balloons. Passing current through two wires in opposite directions produces opposing magnetic fields. Scaling this up, the Generation 2 design uses two sets of cables — one on the ground and another affixed above and running along with the elevated launch tube. Passing tens of mega-amperes through each cable produces magnetic fields sufficient to keep the launch tube pressing upward against the tethers that hold the entire mega-structure affixed to the Earth.
StarTram designers expect the Generation 1 and 2 could be built over a period of 10 and 20 years, respectively, at costs of $20 billion and $60 billion.
Litz Wire Powers Magnetic Levitation
Many of the maglev applications discussed above rely on Litz wire to get the best possible performance from electromagnets used to produce levitation.
For instance, in one version of the Inductrack II maglev train concept initially developed by Dr. Richard Post and his team at the Lawrence Livermore National Laboratory, a “ladder track” is made entirely from unpowered Litz-wire cables, soldered into bus bars at each end, then encapsulated in stainless-steel cans. This is referred to as a “ladder track” because the cables are laid across the track, perpendicular to the train’s motion of travel. As a Halbach array of magnets affixed to the train passes over the Litz-cable track, it induces currents in the cables that, in turn, produce a magnetic field that lifts the train. No external power whatsoever is required, but for a small auxiliary “push” to get the train moving. Nor does this design require cryogenics to supercool permanent magnets. At least one company competing to build Elon Musk’s people and cargo mover, the 750 MPH Hyperloop, has proposed using the Inductrack technology.
In a more general sense, Litz wire plays a key role in all kinds of electromagnetics. Electromagnets produce fields whose strength is proportional to the current and frequency of the A.C. power used. However, at higher frequencies, ordinary magnet wire suffers losses from skin effect and proximity effect that appear as unwanted heat. Litz wire drastically reduces those as well as eddy current losses. It allows for lower operating temperatures and avoidance of “hot spots.” Electromagnets, in fact, any coil windings, using Litz wire allow for smaller footprint and compact designs that offer substantial weight reduction compared to ordinary magnet wire.
New England Wire Technology has delivered Litz wire to the electronics industries for more than a century. In recent years the company has developed proprietary fabrication techniques that reliably process round Litz constructions into various cross sectional geometries—all without damage to individual strands or their insulation, and all are backed by the company’s extensive quality assurance programs. Learn more about how Litz wire can improve your design, or contact us to speak with an engineering representative.
Custom Design
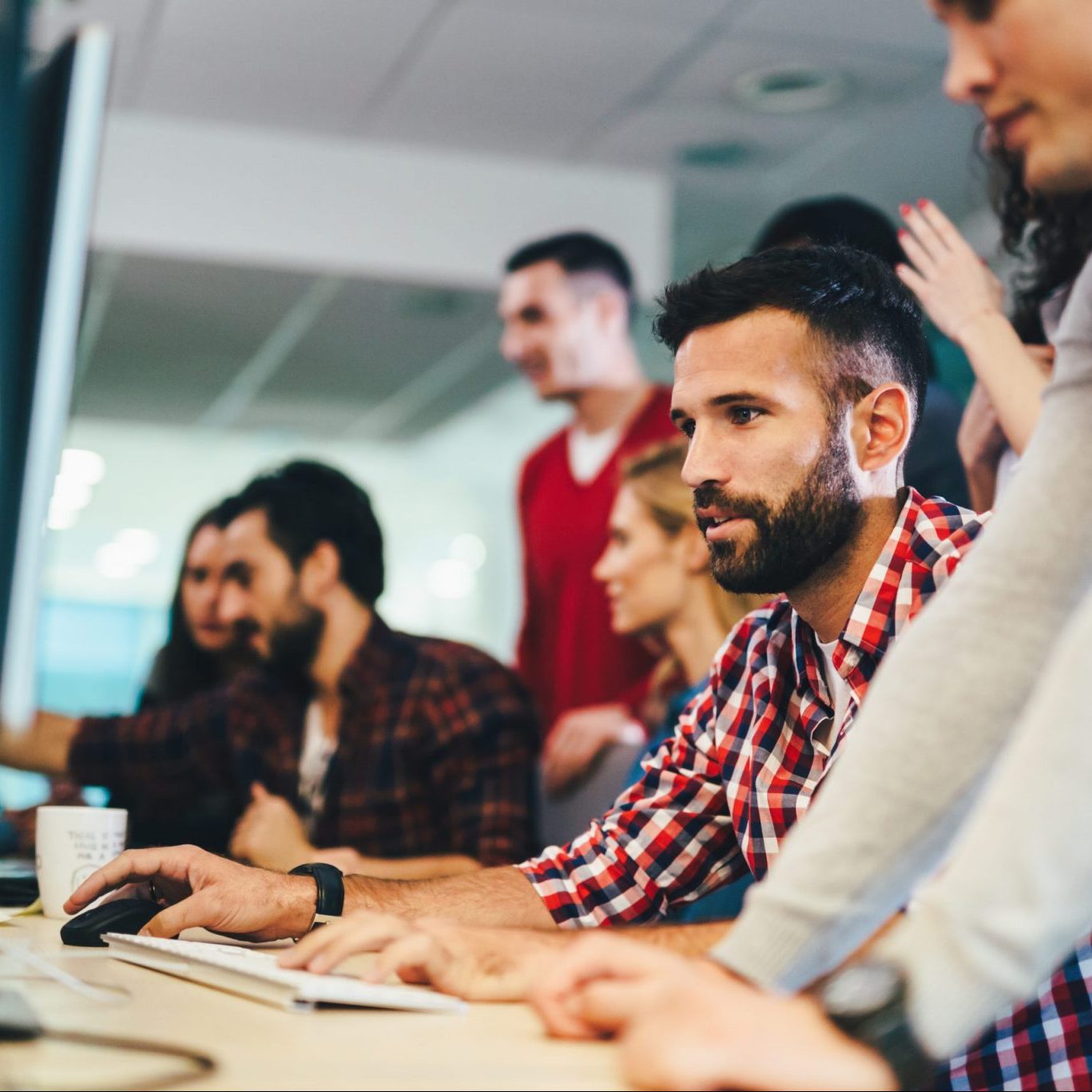
About Our Engineers
Innovative solutions start with an experienced team of engineers, armed with the latest design tools and technology. Our focus on understanding the individual, complex challenges of our customers and designing solutions that fit, is why we have been trusted as the industry leader for over 100 years.